Prêts pour la transition énergétique ?
Participer à la transition énergétique est plus que jamais nécessaire.
C’est LA solution à mettre en place pour la planète mais aussi pour le portefeuille.
Car c’est en combinant les petits et grands gestes au quotidien qu’on arrivera à diminuer
notre consommation, réduire notre facture d’énergie et contribuer à un avenir neutre en carbone.
Nos actualités
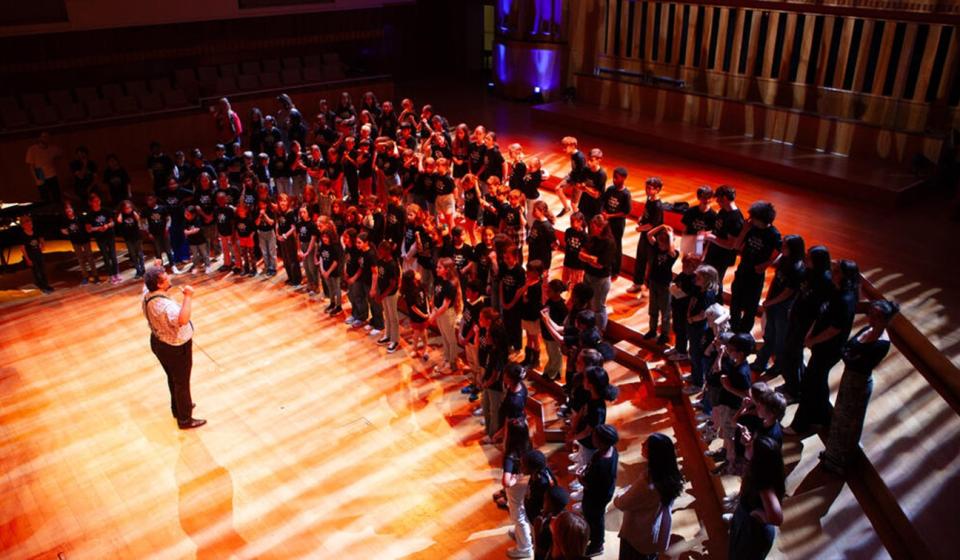
ENGIE et la Flagey Academy font chanter la jeunesse bruxelloise
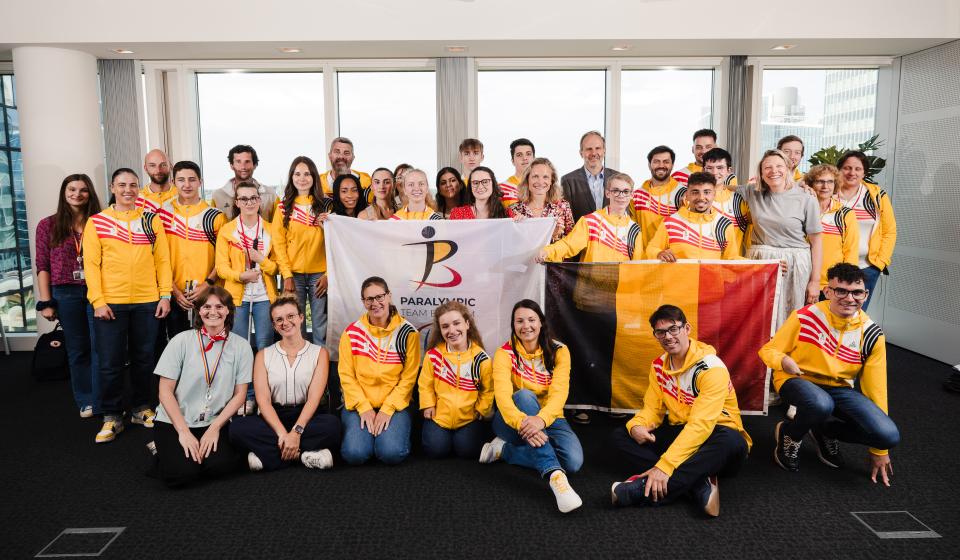
ENGIE accueille la délégation belge des European Para Youth Games 2025
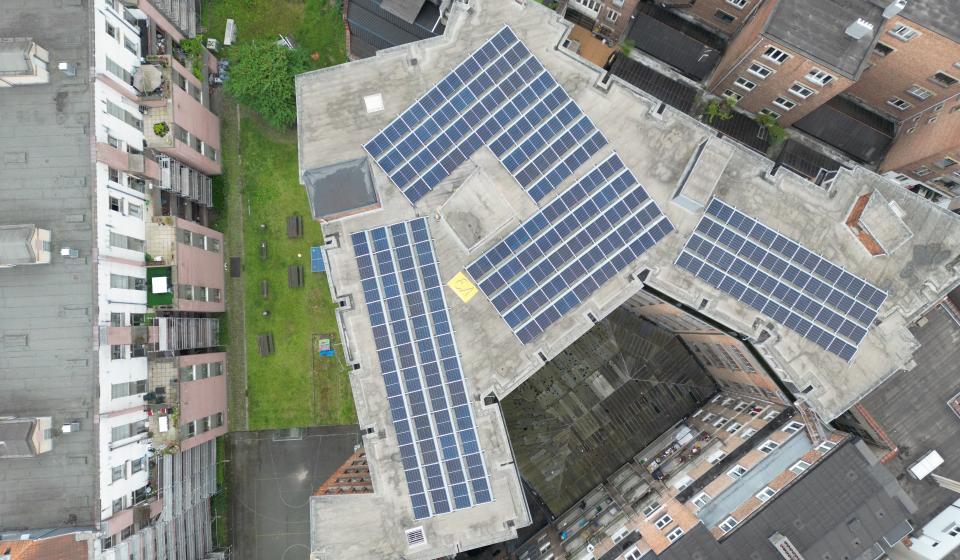
168 panneaux solaires pour un avenir plus durable et solidaire à l’Armée du Salut
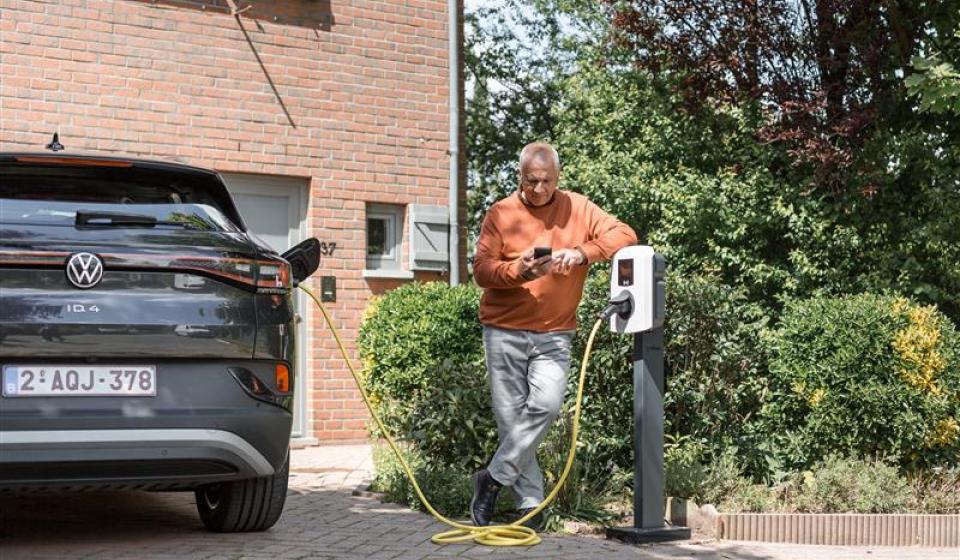
ENGIE récompense la flexibilité de ses clients et introduit un nouveau contrat d'énergie avec des heures super-creuses
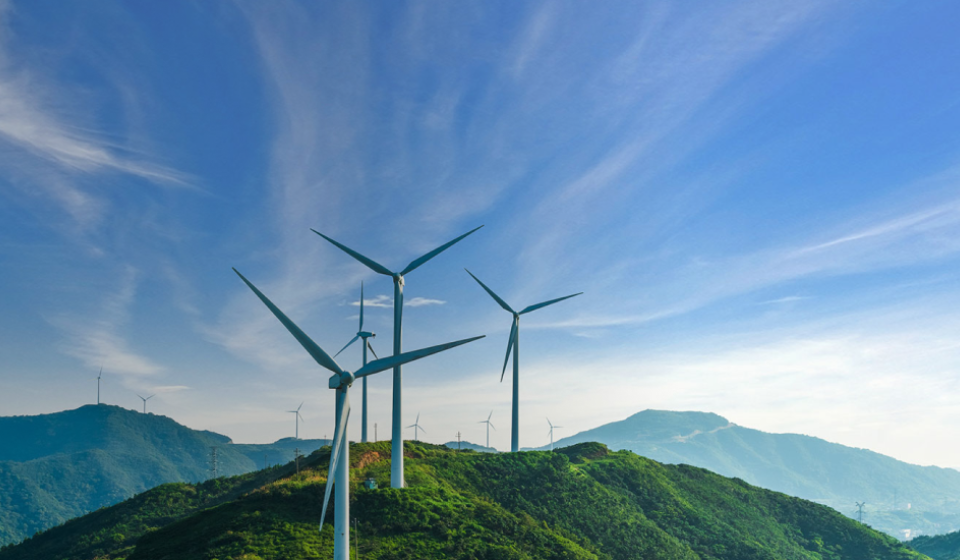
A la recherche d'informations sur un parc éolien près de chez vous ?
Suivez toutes les mises à jour des parcs éoliens ici.

Vrai ou faux?
Envie de tester tes connaissances sur les éoliennes? Participe à notre quiz afin de découvrir le vrai du faux.
Nos activités
ENGIE est une entreprise de référence dans le domaine de l'énergie et des services, avec un large éventail d'activités. Découvrez-les ici.

"Chez ENGIE, nous avons un réel impact sur l'accélération de la transition énergétique"
Avec mes collègues, nous gérons les chantiers de construction des parcs éoliens.
Après mes études, j'avais vraiment envie de travailler dans les énergies renouvelables. C’est hyper intéressant mais aussi dans l’air du temps puisque l’éolien contribue concrètement à la transition énergétique.
Nous avons l’objectif de fournir plus de 2 milliards de kilowattheures, grâce à 350 éoliennes terrestres à l'horizon de 2030. Soit l’équivalent de la consommation annuelle de 570 000 ménages. Cela représente une réduction d’émissions de CO2 de 900 000 tonnes. Nous voulons atteindre le Net Zéro Carbone d’ici 2045.